Production Of Glass
Production Production Of Glass

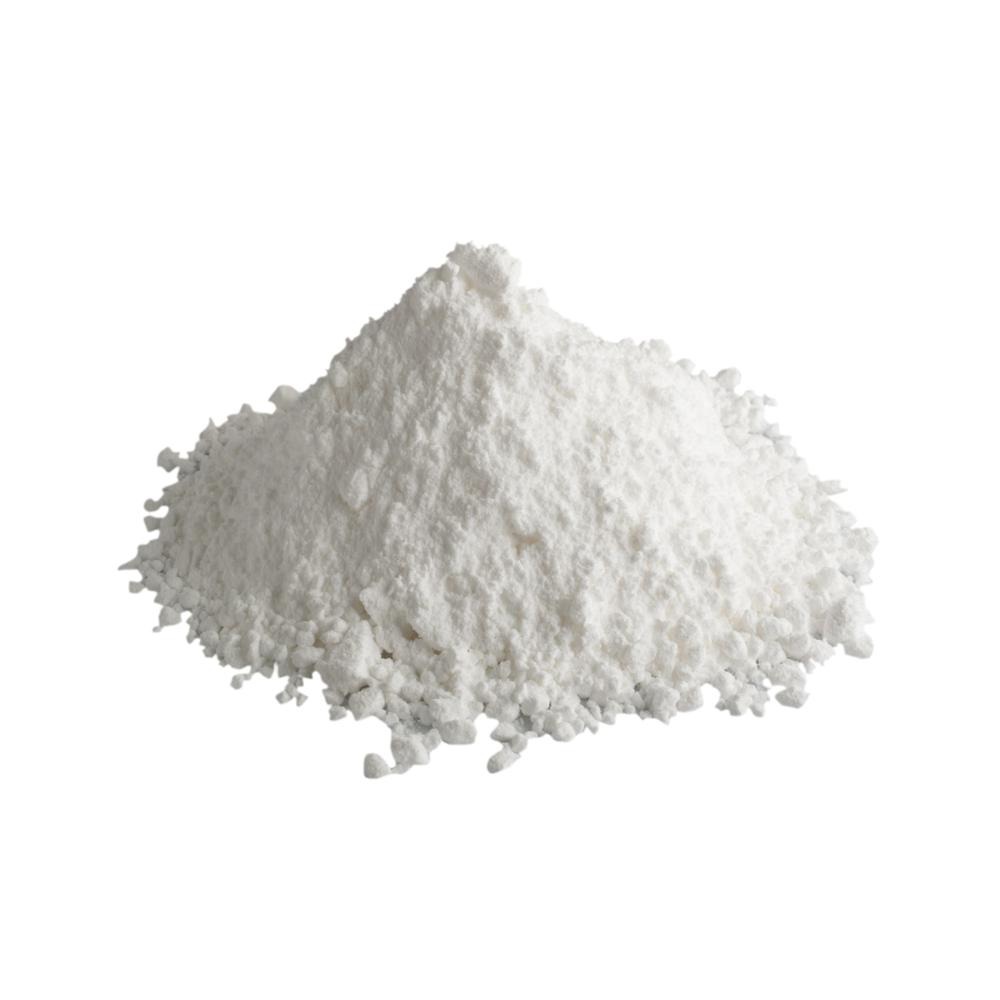
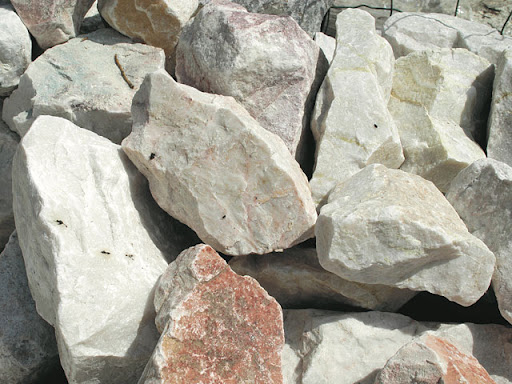
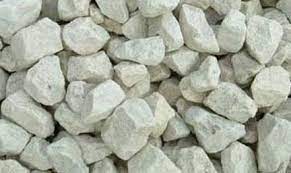
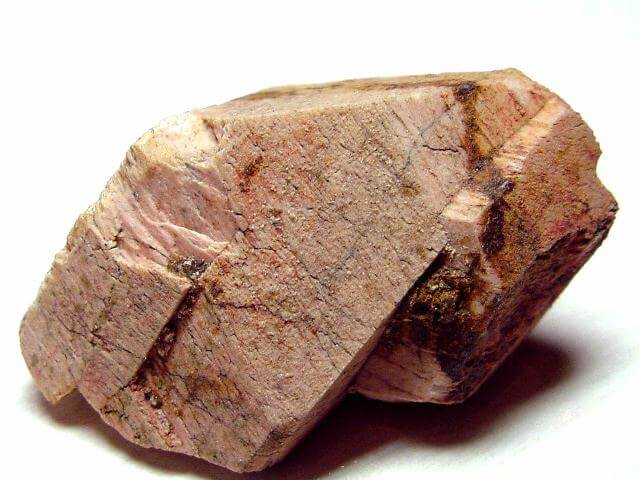
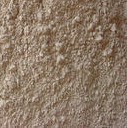
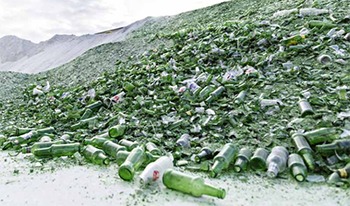
Hot coating process is applied to glass packages immediately after forming machines. The purpose of this process is to close the micro cracks in the bottles and to create a primer for the Cold Coating process that will be applied after the annealing furnace.
During forming, glass packages are loaded with undesirable tensions that reduce their strength as they cool suddenly and uncontrollably. Annealing furnaces are used in order to eliminate the resulting stresses (tension) by controlled cooling (annealing).
1- Glass packages with cold coating liquid are subjected to various controls and tests by sampling method (visual control, gauge control, pressure and impact control).
2- All of the products coming from the forming are passed through the latest technology defect separation machines for head, bottom, side surface, crack, mouth sealing and narrow neck control.
3- Samples are taken from the products that pass through the defect sorting machines, final visual controls are made by both online machines and operators, and they are sent to the packaging after the approval of the quality department.
The error is corrected by instant notification of the found errors to the forming area. At the same time, faulty glass packages are discarded and recycled in order to feed them back into the furnace.